Welded pipe forming technology is an indispensable part of modern industry. Especially in the application of used welded pipe units, the rebound problem has always troubled producers and technicians. Springback not only affects the dimensional accuracy and surface quality of welded pipes, but may also cause cracks and welding defects, thereby affecting the overall performance and service life of welded pipes. Therefore, how to overcome the rebound problem during welded pipe forming has become the key to improving the quality and efficiency of welded pipe production.
1. Springback phenomenon of welded pipe forming and its causes
Welded pipe forming is a complex plastic deformation process, which includes both elastic deformation and plastic deformation. Springback is caused by the failure of the elastic deformation part to fully recover after plastic deformation. When the metal strip is subjected to external force during the forming process, elastic deformation and plastic deformation will occur. After the external force is removed, the elastic deformation part will recover quickly, resulting in a difference between the actual shape of the welded pipe and the expected shape, that is, springback.
The springback phenomenon is mainly manifested in the following aspects in the forming of welded pipes:
Inconsistent hole design: When the forming roller is designed according to the hole design method, due to the existence of springback, the actual final forming shape is not the required shape, especially the forming of the edge of the strip is often insufficient, resulting in the cross-sectional shape of the welded pipe deviating from the design standard.
Weld crack: When producing alloy welded pipes at high speed, large springback will cause cracks in the weld that has not been completely solidified when leaving the extrusion roller, seriously affecting the welding quality and strength of the welded pipe.
Welding cannot be carried out: In order to increase the welding speed of alloy welded pipes, the two edges of the pipe blank need to be in close contact. If the springback is large, the pipe blank will open at the front and rear edges of the extrusion roller, making welding impossible and affecting production efficiency.
2. Main factors affecting the springback of welded pipe forming
The springback of welded pipe forming is affected by many factors, including material properties, forming process parameters and equipment conditions.
Material properties
Elastic modulus: Elastic modulus is a physical quantity that measures the material's ability to resist elastic deformation. Although the elastic modulus of steel materials is not very sensitive to slight changes in chemical composition and changes in microstructure, there are still certain differences in the elastic modulus of different materials. Generally speaking, the larger the elastic modulus, the smaller the rebound; conversely, the larger the rebound.
Yield strength: The yield strength of the material is an important factor affecting the rebound. The higher the yield strength, the more difficult it is for the material to undergo permanent deformation during plastic deformation, and the greater the rebound. Therefore, the rebound of low-carbon steel is relatively small, while the rebound of low-alloy steel and alloy steel is large.
Work hardening: During the forming process of welded pipes, metal materials will undergo work hardening, that is, as the deformation increases, the yield strength and hardness of the material will increase. Work hardening will increase the rebound tendency of the material, making the rebound problem more difficult to solve.
Forming process parameters
Deformation: The deformation of the metal during the forming process has a significant effect on the rebound. The larger the deformation, the greater the proportion of the plastic deformation part of the material, and the smaller the rebound. However, excessive deformation will increase the load and energy consumption of the equipment, and may even cause the material to rupture.
Forming speed: The faster the forming speed, the shorter the deformation time of the metal material, the less time the plastic deformation has to develop fully, and the greater the springback. Therefore, under high-speed production conditions, the springback problem is more prominent.
Forming temperature: Temperature is an important factor affecting the plasticity and deformation capacity of the material. Forming at an appropriate temperature can reduce the yield strength and work hardening degree of the material, thereby reducing springback. However, too high a temperature may cause oxidation and decarburization of the material, affecting the quality of the welded pipe.
Equipment conditions
Forming roller design: The design of the forming roller has a great influence on springback. Reasonable forming roller shape and size can reduce the springback tendency and improve the forming quality of the welded pipe.
Equipment accuracy: The accuracy and stability of the equipment also have an important influence on the forming quality of the welded pipe. Insufficient equipment accuracy or poor stability will lead to increased errors and fluctuations in the forming process, thereby increasing the possibility of springback.
Lubrication conditions: Good lubrication conditions can reduce friction resistance and energy consumption in the forming process, which is conducive to reducing springback. However, the selection and use of lubricants need to be cautious to avoid adverse effects on the quality of the welded pipe and the environment.
3. Methods to overcome the springback of welded pipe forming
For the springback problem of welded pipe forming, a series of measures can be taken to reduce the springback from the aspects of material selection, forming process optimization and equipment improvement.
Optimize material selection
Select low-springback materials: When possible, give priority to materials with small springback, such as low-carbon steel. These materials have low yield strength and good plastic deformation ability, which is conducive to reducing springback.
Improve material properties: Improve the properties of materials by heat treatment, alloying and other means, reduce their yield strength and work hardening degree, thereby reducing springback. For example, normalizing low-carbon steel can improve its plasticity and toughness, which is conducive to reducing springback.
Optimize forming process parameters
Adjust the deformation amount: Under the premise of ensuring the quality of the welded pipe, appropriately increase the deformation amount in the forming process, increase the proportion of the plastic deformation part, and thus reduce the springback. However, the increase in deformation needs to be controlled within a reasonable range to avoid material rupture and excessive equipment load.
Control the forming speed: Under high-speed production conditions, the springback can be reduced by reducing the forming speed. Reducing the speed can prolong the deformation time of the metal, allowing the plastic deformation to fully develop, thereby reducing the tendency of rebound.
Adjust the forming temperature: Forming at an appropriate temperature can reduce the yield strength and work hardening degree of the material, thereby reducing rebound. However, the choice of temperature needs to comprehensively consider factors such as the performance of the material, the conditions of the forming equipment, and the production environment.
Improve equipment design
Optimize the design of the forming roller: According to the properties of the material and the requirements of the forming process, the shape and size of the forming roller are reasonably designed. Rebound can be reduced by increasing the deformation of the forming roller and adjusting the gap between the rollers. At the same time, the surface quality and accuracy of the forming roller also need to be strictly controlled to ensure the stability and accuracy of the forming process.
Improve equipment accuracy and stability: Strengthen the maintenance and maintenance of the equipment to improve the accuracy and stability of the equipment. Regularly inspect and calibrate the equipment to ensure that the errors and fluctuations in the forming process are within the controllable range.
Improve lubrication conditions: Select appropriate lubricants and use them reasonably to reduce friction resistance and energy consumption during the forming process. At the same time, it is necessary to pay attention to the impact of lubricants on the quality and environment of welded pipes, and avoid using lubricants that are harmful to the environment.
Use advanced forming technology
Preforming technology: Preforming is one of the more commonly used processes in pipe filling and hydraulic forming. Preforming can change the initial state of stress and deformation of the subsequent hydraulic forming of the pipe, and have a certain impact on the springback of the hydraulic forming of the pipe. Therefore, it is possible to try to use preforming technology to reduce springback. However, the specific effects and parameters of preforming technology need to be studied and optimized according to actual conditions.
Flexible forming technology: Flexible forming technology is a new forming method that uses flexible molds instead of traditional rigid molds for forming. Flexible molds can be deformed and adjusted according to the properties of the material and the requirements of the forming process, so as to better adapt to the deformation process of the material and reduce springback. However, the cost of flexible forming technology is high and the technical difficulty is high, which requires continuous exploration and improvement in practical applications.
Use springback compensation measures
Springback prediction and compensation: Use advanced numerical simulation methods such as finite element analysis to predict and calculate the springback in the welding pipe forming process. According to the prediction results, the forming process parameters and equipment conditions are adjusted and optimized to compensate for the impact of springback. This method requires a high level of technology and computing power support, but it can improve the forming quality and precision of welded pipes to a certain extent.
Online detection and adjustment: Introduce an online detection and adjustment system during the forming process of welded pipes to monitor the shape and size changes of welded pipes in real time. According to the test results, the forming process parameters and equipment conditions are adjusted and optimized in real time to reduce springback and improve the forming quality of welded pipes. This method requires the support of advanced sensors and control systems, but it can achieve automation and intelligent control in the production process.
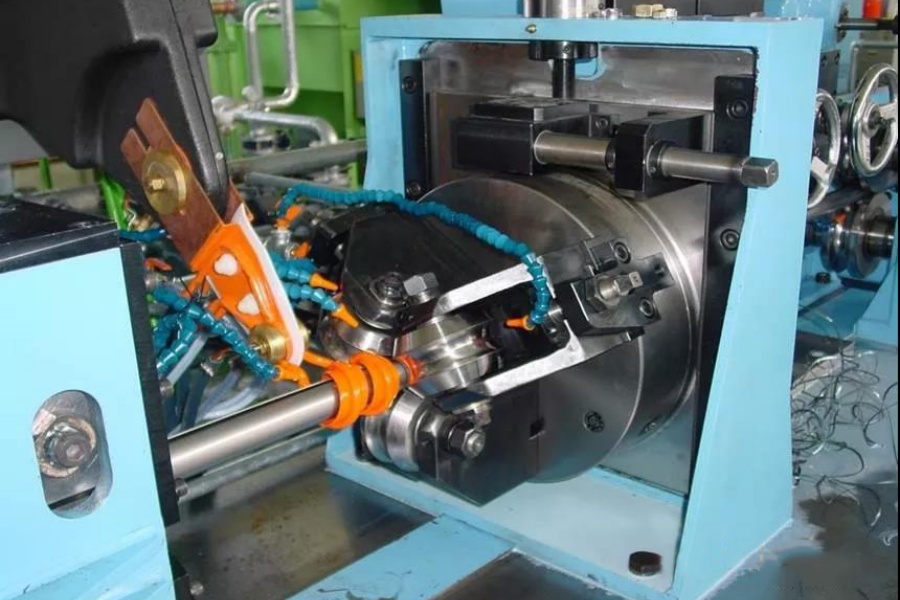
Welded pipe forming springback is a complex problem affected by many factors. In order to overcome the springback problem during the forming of used welded pipe units, it is necessary to start from material selection, forming process optimization and equipment improvement, and take a series of measures to reduce springback. At the same time, it is also necessary to continuously explore and apply new forming technologies and springback compensation measures to improve the forming quality and production efficiency of welded pipes.
In the future development, with the continuous progress and innovation of materials science, forming technology and intelligent manufacturing technology, it is believed that the springback problem of welded pipe forming will be more effectively solved and overcome. This will provide strong technical support and guarantee for the sustainable development and industrial upgrading of the welded pipe industry.