In industrial production, welding pipe equipment, as an important part of the production process, bears the heavy responsibility of welding and processing pipes. However, long-term use of welding pipe equipment is prone to various problems, such as wear of parts and aging of structures, which will directly affect production efficiency and product quality. Therefore, it is particularly important to carry out core renovation of Used Welded Pipe Machine.
Disassembly and cleaning are the first step in renovation. Decompose the equipment into independent modules, such as forming units, welding machines, sizing machines, cutting devices, etc., so as to facilitate deep processing. During the cleaning and rust removal process, use high-pressure water guns or chemical cleaning agents to remove oil and rust, and use ultrasonic cleaning for precision parts to avoid physical damage; sandblast or shot blast the structural parts to completely remove the oxide layer.
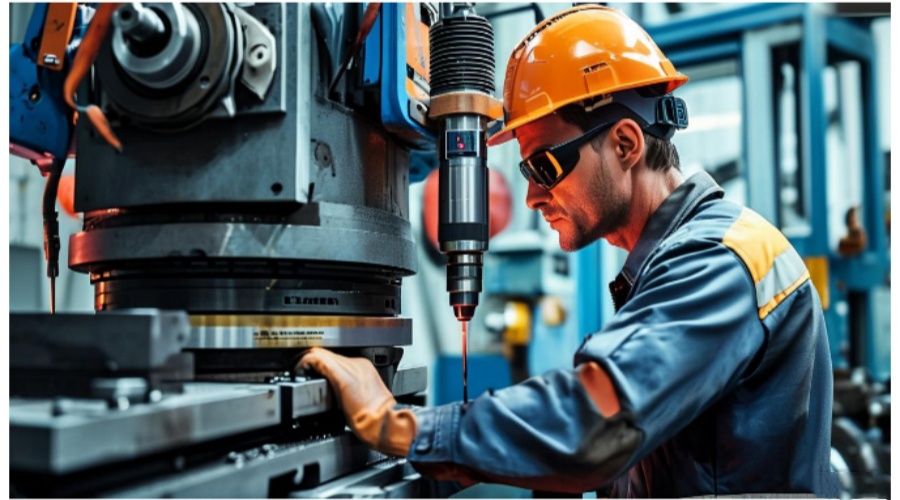
The renovation of the mechanical system is the key to ensuring the performance of the equipment. First, replace the worn parts, such as rollers, bearings, gears, chains and belts, and choose original or highly compatible substitutes. For the worn surfaces of transmission parts such as guide rails and lead screws, they can be repaired by chrome plating or laser cladding. Next, calibration and adjustment work is also crucial. Use a laser calibrator to adjust the parallelism of the rolls and the coaxiality of the unit, and perform dynamic balancing detection on rotating parts such as flying saws to avoid vibration during high-speed operation. The lubrication system also needs to be modified, clean or replace the blocked oil circuit, and upgrade to a centralized automatic lubrication system.
Upgrading the electrical and control systems can improve the overall performance of the equipment. Update electrical components, including replacing aging circuits, relays and contactors, and upgrading to energy-saving motors or servo drives. At the same time, check and repair welding power supplies, such as high-frequency generators and arc stability. The transformation of the control system includes upgrading traditional PLCs to modern models such as Siemens or Mitsubishi to improve response speed and compatibility. Install a human-machine interface (HMI) to achieve visual adjustment of parameters, integrate intelligent sensors, and increase fault warning functions.
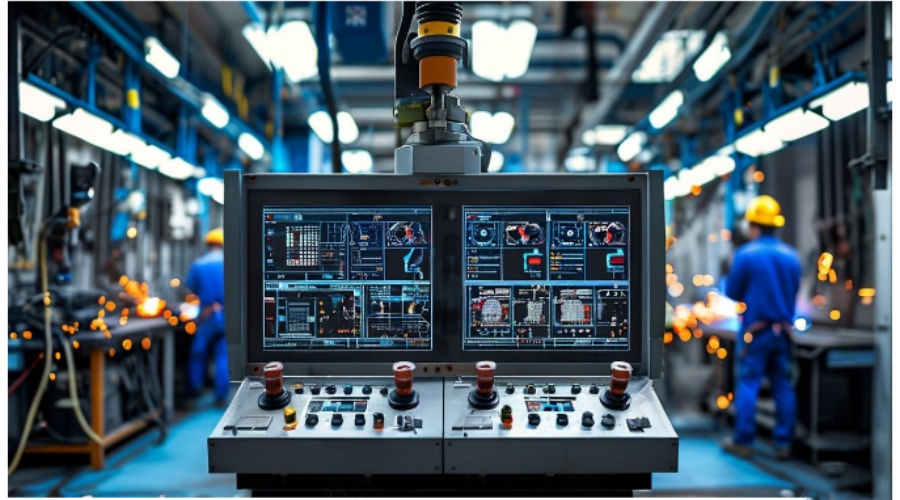
Special repairs of welding and cutting units are equally important. Clean the welding gun nozzle, repair the insulation layer, replace the damaged wire guide tube, and calibrate the welding current/voltage to ensure the uniformity of the weld. For the cutting system, repair the synchronization accuracy of the flying saw, adjust the cutting cylinder or servo positioning, and replace the blunted blade or laser cutting head.
The appearance and protection treatment of the Used Welded Pipe Machine are not only for beauty, but also for extending the service life of the equipment. Correct the deformed frame or strengthen it with local repair welding, spray anti-rust primer and wear-resistant topcoat, and mark the key operation area. Safety protection devices such as protective covers, emergency stop buttons and gratings are also indispensable.